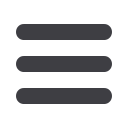
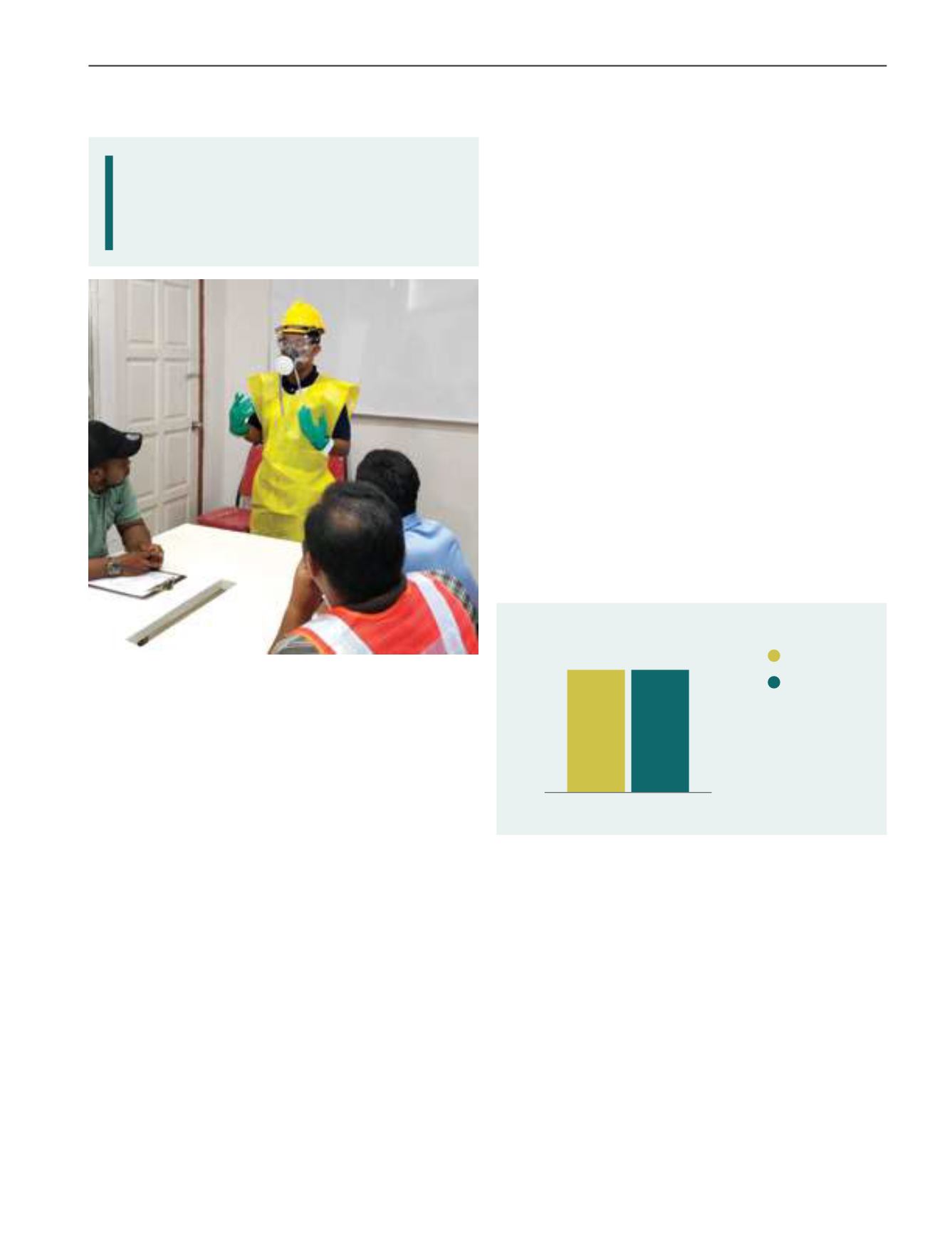
Fima CORPORATION Berhad
(197401004110) (21185-P) •
Annual Report 2020
61
26.7%
of the employees have been in employment with the
Group for 10 years or more
Occupational Safety & Health
Operating safely, sustainably and responsibly remains integral to
us and contributes towards the long-term success of our business.
Our aim is to continually build and instil both a company and
industry culture that protects people from harm and improves
their health and wellbeing.
Towards this end, we comply with all the relevant national laws,
regulations and other requirements relating to best practices
in occupational safety and health; and continuously carry out
activities aimed at preventing workplace injuries. Preventive and
scheduled maintenance is regularly performed on all the Group’s
facilities, plants, storage tanks and terminals, whereupon repairs
and replacements are made when necessary or appropriate. In
addition, contractors and third party service providers working
for and employed by the Group are responsible for knowing and
complying with all applicable laws, regulations, approvals or
permits relating to the work they are doing for the Group. Those
found to be in breach of these requirements would be subjected
to suspension and/or termination of their services.
Employees who use any machinery are trained to do so correctly,
while training programs in the use of personal protective
equipment for workers handling or exposed to hazardous
materials are conducted regularly and will continue to be a vital
part of the Group’s operations.
All division’s have health and safety committees which consist of
divisional management and employees. It is to these committees
that incidences are reported, and where compliance with policies
is monitored, and improvements are discussed.
In our Manufacturing Division, for instance, all chemical related
product supplied are issued a Safety Data Sheet (“SDS”). This
sheet clearly indicateds the type of chemical that employees
are being exposed to and how best to handle them. The SDS will
indicate the potency of the chemical and the level of danger it
may pose to the employee i.e. mild, moderate, highly dangerous.
The safety measures taken by the employee will commensurate
with the danger level.
Manufacturing Division
has achieved 2,015 days (which is
equivalent to 5.5 years) without any lost time incident as at 31
March 2020. During the year in our Plantation Division, PTNJL’s
palm oil mill has retained its accreditation of
System Manajemen
Keselamatan dan Kesehatan Kerja
(or “SMK3”), a local Indonesian
Government safety certification that is comparable with the
globally recognised OHSAS 18001:2007.
FYE2019
FYE2020
Occupational Fatalities
1
1
FYE2020
FYE2019
Tragically we suffered one fatality in FYE2020. In November
2019 an employee at our PTNJL oil mill was fatally injured while
trying to remove some dirt near the mechanical nut stirrer. As a
company standard, we offered support to the bereaved family
and conducted investigations. This incident had served to remind
us that we must continue to strive to make our workplaces safer
and our employees cognisant of the risks in their respective job
functions.
Lost Time Injury
Beginning FYE2020, we have applied the methodology of the
Malaysian Department of Occupational Safety and Health in
computing our Lost Time Injury Frequency Rate (“LTIFR”). The
methodology takes into account only those who are absent from
work for more than 5 working days.
sustainability : social